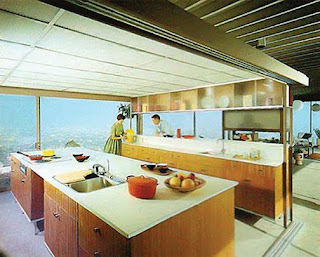
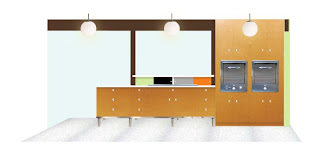
We gave our drawings and a pic of the Case Study #22 kitchen to our cabinet guy, wrote him a check and hoped he would do a good job. Haley was having nightmares of Swiss Chalet, rustic cabinets with wood burned accents.
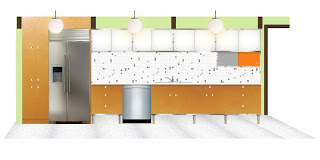
This is what we saw when we came back 2 hours later.
This was our first view of how it was all going to fit together. Those upper cabinets really set things off... as do the legs.
(note: they originally made the back of the cooktop/spicerack cabinet go all the way to the floor. We wanted everything up for a more cohesive look and allow light from one room to spill into the other, so they removed the spice rack, took it back to the shop to cut and trim it down.) The sliders of the spice rack are paint grade plywood that Haley and I will paint to match our drawing at the top of this post.
All cleaned up with temporary melamine countertops tacked in place. They will work until we decide on the right solid surface counters (right= affordable and good looking).
The sink will go where the blue paper towels are, and the hole on the left will be filled with the under-counter microwave.
This is my favorite view. Those holes will be covered by the backing that is attached to the spice rack, which was removed to trim 8" or so off the bottom. The wood sliders under the glass uppers will be painted to match the drawing at the top of this post.
Next, install the fridge, dishwasher, sink, disposer, twin ovens, cooktop and microwave.
Phase 2 will include permanent countertops and the under-counter food processing center thingie.